Pressure testing is a topic where a number of myths and misunderstandings have developed in the swimming pool industry. Below, we explain the truth behind 4 common misconceptions that should help you stay focused on efforts that will lead to leak detection success and profits.
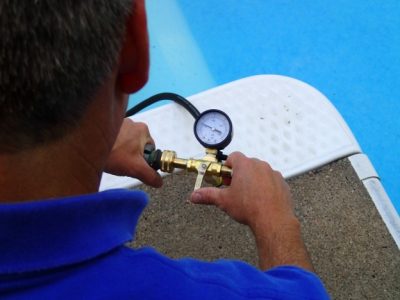
MYTH #1: Pressure Testing is Unnecessary for Leak Detection
While you may be able to find common leaks without pressure testing, if you want to leave the pool assured that you have found all of the leaks . . . and you want to give the customer that assurance, pressure testing is critical.
There are other ways of finding easy to reach leaks in plumbing, but from the standpoint of conclusively determining if the entire line is leak free, nothing beats a properly performed pressure test. Furthermore, despite advancements in cameras and other probes that have applications in some situations, the most common and dependable way of pinpointing leaks underground involves the use of a listening device that picks up the sound of pressurized air escaping from a leak into water saturated soil.
MYTH #2: Air Can Be Used Interchangeably With Water for Pressure Testing
Air and water behave very differently in pressure testing situations. Understanding three pressure testing principles that address these differences is important as you determine when to use air and when to use water to build pressure.
- Air compresses under pressure, water does not
- Air stays at the top of the pipe, water stays at the bottom
- Air escapes from leaks faster than water does
Our pressure testing slide show provides helpful diagrams and more explanation of how these principles affect your test results. As a general rule it is best to use water when testing to determine if the line is leaking since it does not compress under pressure so it will show a loss in pressure quickly, even with a small loss in volume. On the other hand, air trapped in a line can expand as water volume is lost from the leak, slowing (and sometimes completely masking) a drop in pressure. Additionally, if plugs happen to pop out under pressure they will come out with much less force if the line is pressurized with only water . . . trapped air will propel a popped plug like a cannon ball!
The main benefit of using air is that it makes a much better noise escaping from the pipe into water saturated soil than water does. So, once you have identified a leaking section of plumbing with a water test, switch to air to produce a good noise that can be picked up by your listening device.
Myth #3: Air and Water Can Be “Mixed” in a Pressure Tester and Will Stay “Mixed” Inside the Pipe
We’ve debunked this myth by testing it on a plumbing system made of clear PVC. Regardless of how they are transmitted into the pipe, water stays low and air stays high. They do not stay mixed up just because they are put under pressure. This is simple physics and anyone who says otherwise is selling you hocus-pocus.
Adding both air and water to a line is not the first step you should take when trying to make a good leak noise. While it is indeed important for the soil to be full of water outside of the pipe where air will blow out through the leak, no noise is made unless air actually gets to the leak. Since water stays at the bottom of the pipe and air at the top, if the leak is in the low end of the plumbing no air will get to it if you are adding both air and water. So, all of the water above the leak level must be purged from the line before this happens. Generally this is best accomplished by removing a low plug and blowing air from the high end. Once you see bubbles, replace the plug, set your air source regulator to maintain no higher than 5 psi, and begin listening. Larger leaks and/or leaks in soil that drains quickly may necessitate adding water while air is going into the line. To avoid noises inside the pipe, do this with a separate pressure tester from the low end of the plumbing. The best results happen when air and water do not mix inside the plumbing . . . just at the leak!
MYTH #4: Certain Kinds of Gas Make Better Noises Than Others for Leak Location
Any gas escaping from a leak will make bubbling/gurgling /hissing/spotting sounds in the full range of sonic frequencies that can be picked up with a listening device. Sometimes, leak detectors will use nitrogen tanks to deliver the gas into the line quietly (without the conflicting sound of a compressor). However, these tanks are used not because of any special characteristic of the gas (in fact, the air we breathe is made up of 78% nitrogen) but because of its ease of availability and inexpensiveness in relation to other gasses. SCUBA tanks adapted with an adjustable regulator can also be used if you can get them filled. A small compressor works just fine for inducing air pressure, especially if you use a 50 foot hose that allows you to position the compressor some distance from where you are listening.
In some situations where soil or leak conditions make it difficult to create a noise helium gas is used to find underground plumbing leaks. In these situations a Helium Detector picks up the presence of the gas as it makes its way to the soil’s surface. Helium is not being used because it makes a better noise, but because it can be detected by this detector.
If you have any questions about pressure testing or swimming pool leak detection, consult the Resource Center of our website or give us a call.